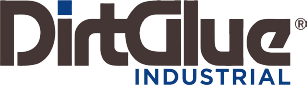
Creating Green Eco-Friendly Hard Surfaces/ Roadways
DGI - THE ORGANIC SOLUTION TO PAVING YOUR WORLD
DGI is a organic based polymer, heavy duty formulation of acrylic polymer specifically engineered for road construction and creating hardened surfaces suitable for all traffic types. DGI is a non-toxic, environmentally safe product which does not contain harmful chemicals and has no adverse effects on
people, animals or the environment making it ideal for application in environmentally sensitive areas.
EXCEPTIONAL RESULTS
DGI has superior UV stability and water repellency making it out perform all competitors. DGI can be applied to all types of aggregates, binding the particles to form a three-dimensional matrix, producing a durable and natural pavement surface. DGI is the ideal choice for natural looking roads, driveways,
hardstand areas, parking lots and pathways.
USES AND BENEFITS OF DIRTGLUE INDUSTRIAL
- Organic Based Polymer
- High UV stability making it long lasting
- Reduced water absorbtion ‹5%
- Non-hazardous and non-toxic
- Ideal for use in environmentally sensitive areas
- For use in rural roads, driveways and Hardstand areas
- Paths for council, golf courses and cycleways
- Construction of BMX tracks, bike and walking trails
- Landscaping and garden construction
- Over 16 years’ experience in the US working alongside the US military and US environmental departments.
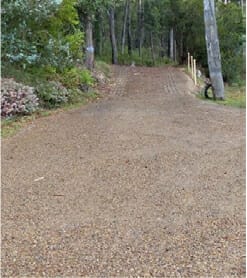
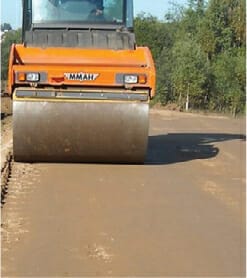

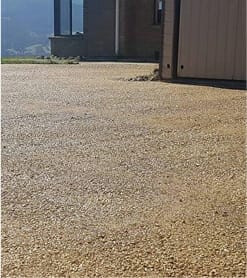
SPECIFICALLY ENGINEERED FOR ROAD BUILDING AND HARD PAVEMENT SURFACES
DirtGlue Industrial Polymer – Over the years, the Polymer industry has had its name tarnished with the distribution of sub-par Polymers being sold and used as stabilisers. These Polymers are wildly inconsistent as they are often by-products of another process (paint manufacture, paper pulp etc.) which are then used as stabilisers. Due to the lack of UV stability, varying concentration of polymers and the polymers H20 re-absorption properties, all factors combine to give the end user a “Russian Roulette”
style result and thus “Polymers” for soil stabilization have in some instances developed a bad reputation…
DGI is a “purpose built” acrylic organic based polymer that has been manufactured with over 16 years’ worth of R&D and working alongside the US military / US environmental industries. Over this time, GES in
the U.S.A has been able to achieve outstanding results regarding this polymer’s stability and durability.
DGI is UV stable and has had its water absorption rate lowered to less than 5%. What this means, is the
Polymer will not break down and deteriorate in the sun and rain, therefore has incredible longevity in its application. This is something other polymer companies cannot claim or substantiate.
In Australia, DGI has been imported under a certification of “an organic based product” which means it was not of a living origin. This is the most environmentally friendly product of its kind and it supports our GREEN solution methodology approach that GES and Green Track strongly believe is the way forward.
With a DirtGlue Industrial application, you will always get a result. How good or strong that result is varies as there are many factors that need to be taken into consideration. The inherent strength of the soil or aggregate used, combined with the workmanship on the base, heavily dictates the overall strength of the substrate and its ability to load bear.
This is an extremely important factor as there is no “one size fits all” application to projects. Each project needs to be approached on a case by case basis and an application method needs to be determined by the applicator. The customer needs to provide parameters and details about the surface’s use, weight it will bear and various other factors that need to be considered by the applicator before a process can be decided upon.
DirtGlue Industrial can be mixed in with “in-situ” soil or all kinds of aggregates but is somewhat difficult to know what result you will get without testing. Where possible, it is preferred to use an aggregate spec
that has been used before and that the applicator is confident with in order to provide the customer with a consistent and predictable result.
As an added benefit DGI is very compatible with TerraDry waterproofing agent. In fact, the TD acts not only to waterproof the individual soil particles when it is blended with DGI during and application it also increases the strength of the overall Polymer Pavement
System by acting on the DGI polymer itself in a crosslinking affect.
"DirtGlue Industrial (Organic Based) Polymer - setting the highest Poly Pavement standards in the world"
New pathway construction Application Guide.
Before you commence your DGI project, it’s crucial that you assess the below key points.
- Penetration of the Polymer – ensure the polymer is evenly distributed through the full depth of the pavement material.
- Compaction – Proper compaction eliminates any voids in the surface and ensure a strong pavement surface
- A good base – Starting your project with a solid, well-formed base will be the foundation for a long lasting surface.
- The right amount of DGI for the job – Using the correct amount of product is essential to achieving the required load bearing outcome.
If you would like further advice on a specific project please contact your local supplier.
Tools
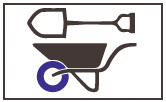
SPADE WHEELBARROW
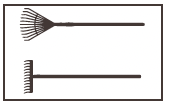
LANDSCAPE RAKE STEEL RAKE

WATERING CAN

HAND COMPACTOR

SCREED & LEVEL
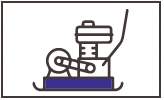
PLATE COMPACTOR
Materials

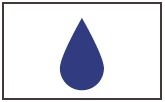
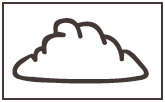
Aggregate Types:
The type of aggregate used will have a direct effect on the strength and durability of the final surface. Crusher Dust or Crushed Granite aggregates are preferred. Green Track Advantage recommends a 5mm-7mm minus crushed aggregate with 20% fines. Refer to Green Track Solutions for more details.
Directions
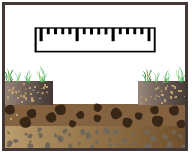
1
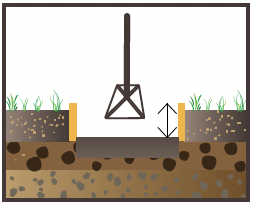
2
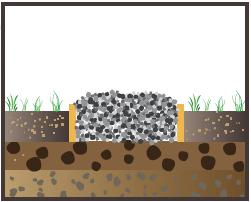
(see Moisture Content Test for further instructions).
3

(see optimum moisture content test for more details).
4
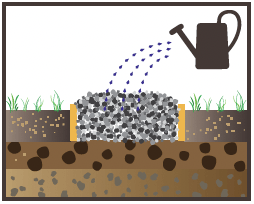
5
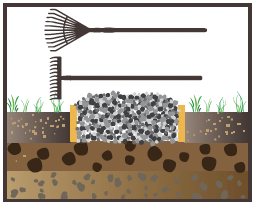
6
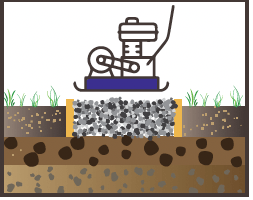
7
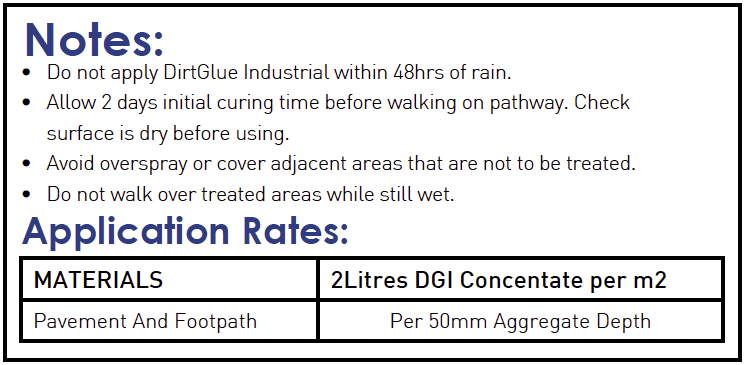
Walking Trail Renovation Application Guide.
Before you commence your DGI project, it’s crucial that you assess the below key points.
- Penetration of the Polymer – ensure the polymer is evenly distributed through the full depth of the pavement material.
- Compaction – Proper compaction eliminates any voids in the surface and ensure a strong pavement surface
- A good base – Starting your project with a solid, well-formed base will be the foundation for a long lasting surface.
- The right amount of DGI for the job – Using the correct amount of product is essential to achieving the required load bearing outcome.
If you would like further advice on a specific project please contact your local supplier.
Tools
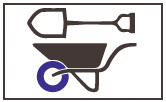
SPADE WHEELBARROW
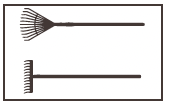
LANDSCAPE RAKE STEEL RAKE

WATERING CAN

HAND COMPACTOR
Materials

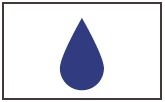
Directions
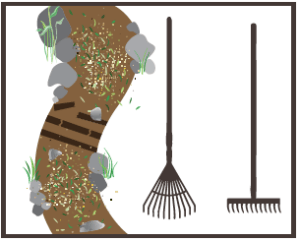
1
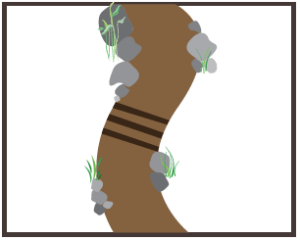
2

3
Calculate the amount of DirtGlue Industrial concentrate required and mix with water. (see mix rates).
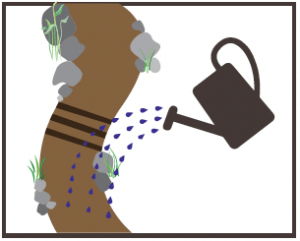
4
Notes:
- Do not apply DirtGlue Industrial within 48hrs of rain.
- Allow 2 days initial curing time before
walking on pathway. - Check surface is dry before using.
- Avoid overspray or cover adjacent areas that are not to be treated.
- Do not walk over treated areas while still wet.
Application & Mixing Rates:
DIRTGLUE INDUSTRIAL TRAIL RENOVATION:
DIRTGLUE APPLICATION RATE
• 2 Litres DGI Concentrate per m² .
DIRTGLUE INDUSTRIAL CONCENTRATE MIX RATIOS
• Mix 1 part DirtGlue Industrial Concentrate with 1 part water.
DIRTGLUE INDUSTRIAL CONCENTRATE
COVERAGE RATE:
• Apply 2L DirtGlue Industrial Concentrate with 2L of water per 1m².